Round Chassis Assembly
Tags: innovate and designPersonhours: 3
Task: Attatch Omni wheels to Round Chassis
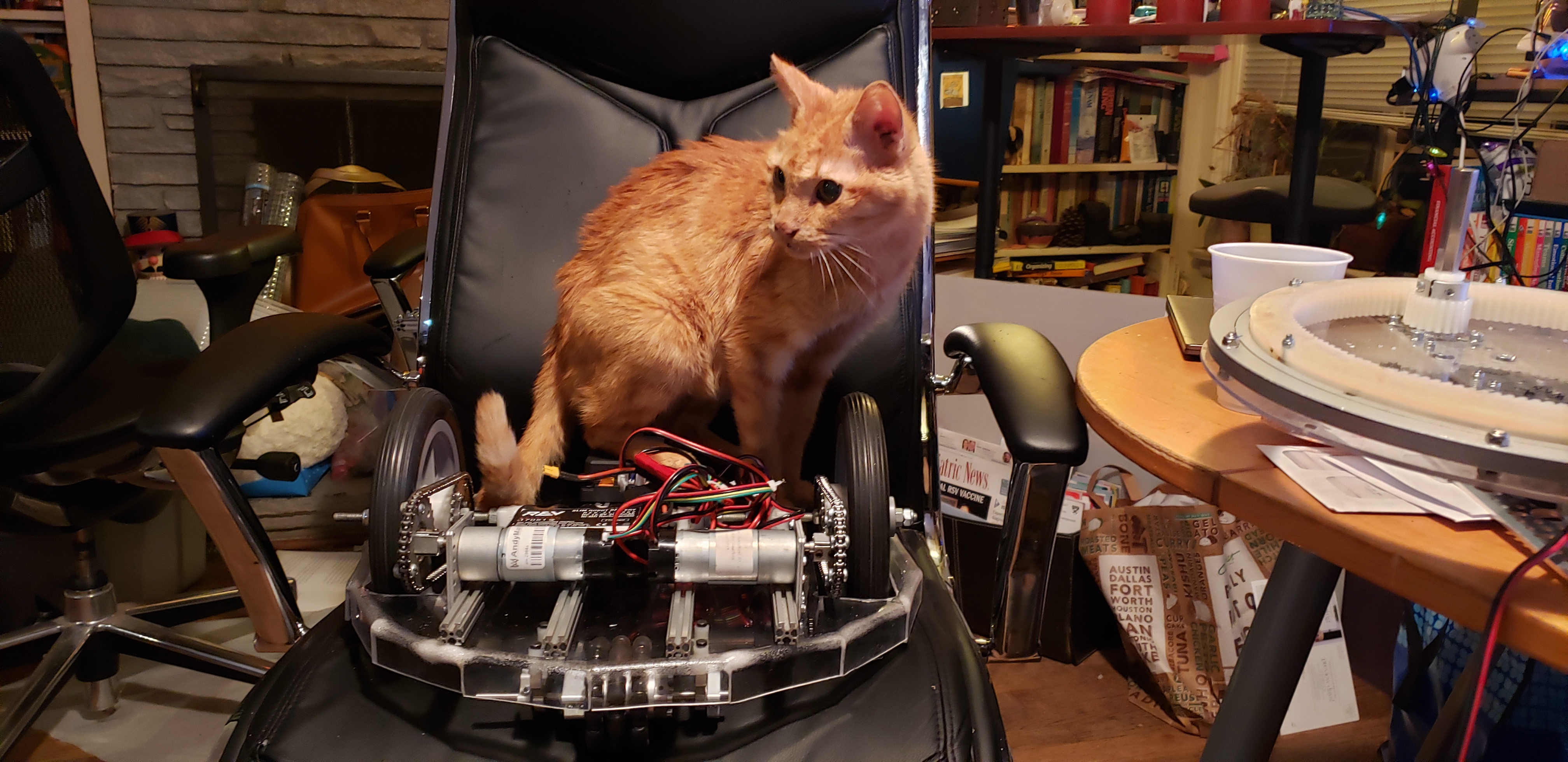
Today we finished assembling the round chassis for our circle robot, TomBot. The most important system we added was the omni wheels to the front and rear of the robot. Without the omni wheels, the robot would tilt like a seesaw around the central 2 big wheels. These omni wheels lightly touch the ground in the front and rear of the robot to keep the chassis parallel with the ground.
The omni wheels were attached so that we have 3 wheels in the front and 3 in the rear. We used 3 wheels to give us more points of contact and more stability at high speeds. The wheels mounted to our new Go Bilda bearing mounts. The mounts have a central bearing with 2 mounting points that branch off of the bearing in a Y shape. The difficulty with this system of mounting the omni wheels is finding the correct height from the polycarb base to mount the bearings. The wheels should be as close as possible to the same height as the 2 big central wheels. The threads in the branches of the Y-shaped bearing mount are very short, which means that almost all the height adjustments need to be done with spacers and long screws. We used the longest screws we had, and after screwing them in to check if the height was right, we found that they were pretty close to what we needed. They still needed spacers to keep the screws from pushing up through the polycarb base, so we used the spacer heights to fine tune the height to get the omni wheels as even as possible with the big wheels. We found that exactly 1 and a half white plastic spacers looked pretty close to the height we needed.
After assembling both sets of wheels, we placed the robot on the field and checked to see how much it tiled back and forth. We found that the 1 and a half spacers was the exact height we needed, as the robot doesn't tilt or wobble at all, and the big drive wheels still have plenty of traction on the field to drive the robot.
These omni wheels allow us to use the chassis to test and work on our other subsystems, but we see some potential flaws in the wheels. The most significant flaw will occur at high speeds. The platform in the middle of the field has a steep edge to it, so driving over it at high speeds will cause those front omni wheels to take a lot of force. Since the mounting is rigid, that force will affect the whole robot and could either jam the robot up against the platform or cause the robot to hop and get shaken up a bit when it drives over.
Next Steps:
One of our modelers is working on 3d printing a suspension system to allow the omni wheels to retract under force. For testing purposes, and for our first qualifier, the rigid system should be fine, but later on the suspension will allow us to move at maximum speed. Our next step is to start assembling the rest of the robot to the chassis.