Caterpillar Track Intake
Tags: design and innovatePersonhours: 12
Task: Build and prototype an intake system
One of the first intake systems we made was the Caterpillar intake assembly (Tetrix tread intake). The inspiration for this design came from an earlier bekt drive comprising of a sander (which you can read about in our earlier post). This was originally built off a c-channel extrusion with a motor attached to sprockets that drive treads. The purpose of this subsystem is to transport the rings from the field into the launcher loading area.
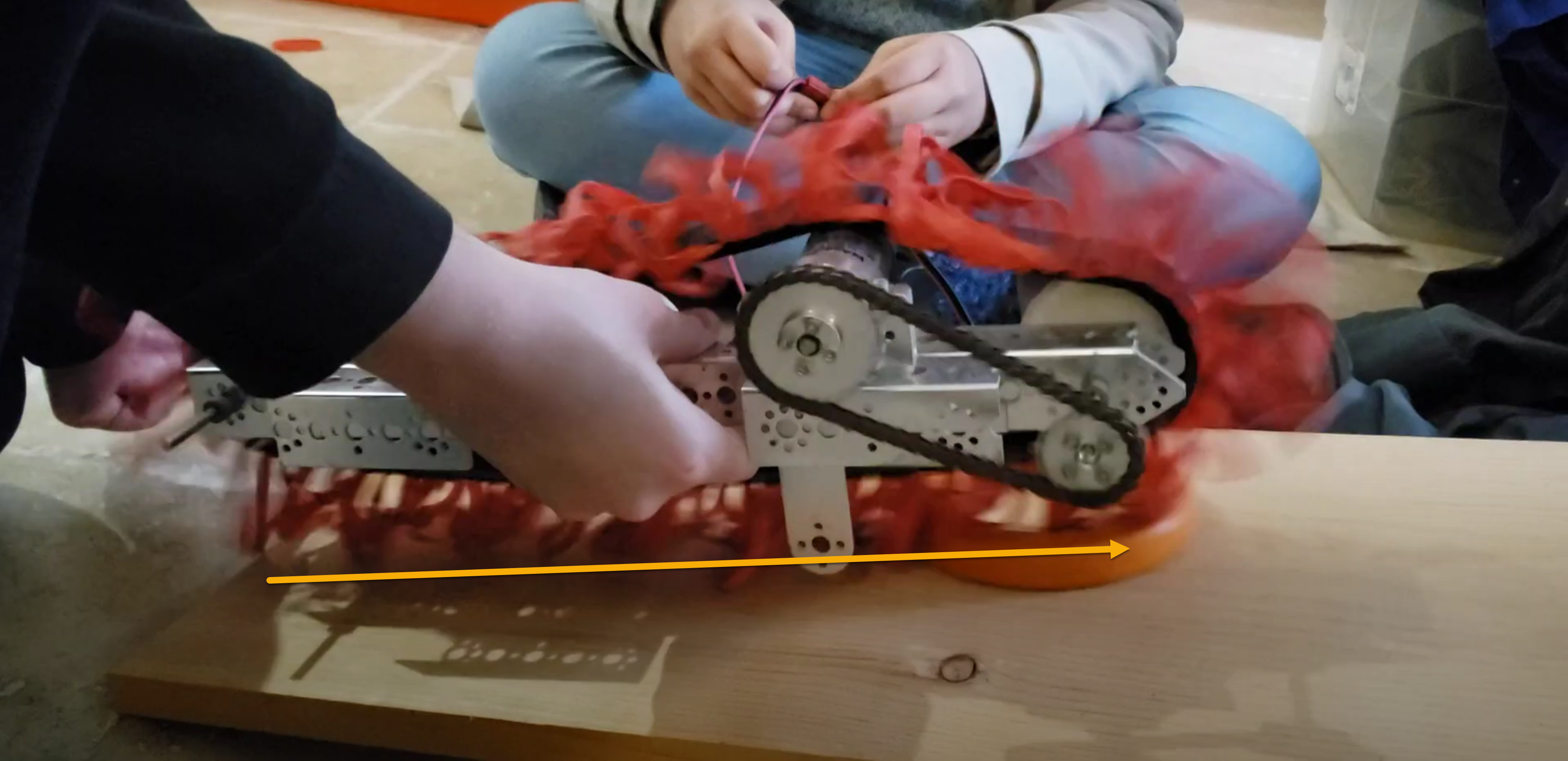
We first tested the assembly without the rubber bands and quickly realized that the treads couldn’t create enough friction to grip the ring and move it vertically. Our solution was to attach rubber bands within each tred piece. There were 2 reasons for this, the first being that rubber in general has high friction and good grip. The second reason is that the flinging rubber bands will conform to the shape of the ring at high speeds and drag the rings up the intake.
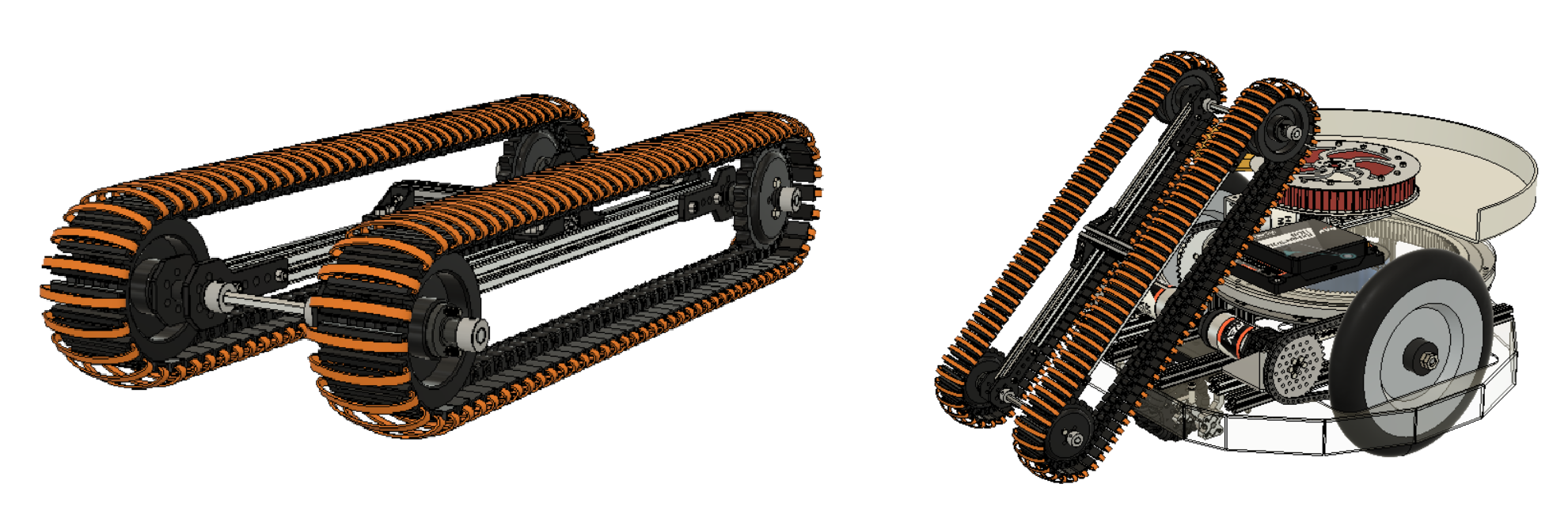
We did experience a few problems with the construction of the assembly. We found that the rubber bands would often get caught on the edges of the c-channel and either fly off at a high velocity, snap, or tangle and prevent the assembly from moving. Because of the way the band fits into a tread, there wasn’t a way to permanently attach the rubber band without damaging the thread, meaning we would have to scrap the idea or find a work-around. We eventually decided to rebuild the intake with REV extrusions because it would be more compatible with our robot and we could replace the large c-channel with the smaller REV extrusions.
Next Steps:
Although this prototype holds promise, we will continue to experiment with it and alternatives to find an alternative that doesn’t run the risk of tangling and disrupting the system.