DPRG Virtual Meeting
Tags: think and connectPersonhours: 15
Task: Present our flywheel launcher to the Dallas Personal Robotics Group
Every year, Iron Reign presents our robot or standout subsystems to the Dallas Personal Robotics Group (or DPRG) - a group of professional robotics enthusiasts based here in Dallas. The DPRG are an organization in Dallas who have monthly meetings for robotics projects In past seasons, we've given them presentations about our seasonal progress in build and code. In an earlier post, we detailed the introduction of our ring launcher - the Flywheel Launcher. Initially, we had only gotten past the CAD design for the launcher, as well machining the plates and 3D-printing its nylon (which we needed to improve the 'gription' of the launcher. But today, we were able to begin the actual assembly and testing of launcher - and we were able to do all of it live on a virtual meeting with DPRG! A link to this presentation is here.
We presented to an audience of around 18. We started off by giving them an introduction into this year's FIRST Tech Challenge game, as well as what goal specifically we were intending to attain with the flywheel launcher. For reference, the flywheel launcher consists of a spinning wheel sandwhiched between two custom-machined plates and as it the robot intakes rings, the spin of the wheels ejects rings with enough force to get it into the goal post. We started off by explaining how the CAD of the design progressed. Considering the multi-staged nature of this subsystem, it required 3 CAD sessions total and we were able to show DPRG each of these stages as well as how we went about the custom-machining of the parts.
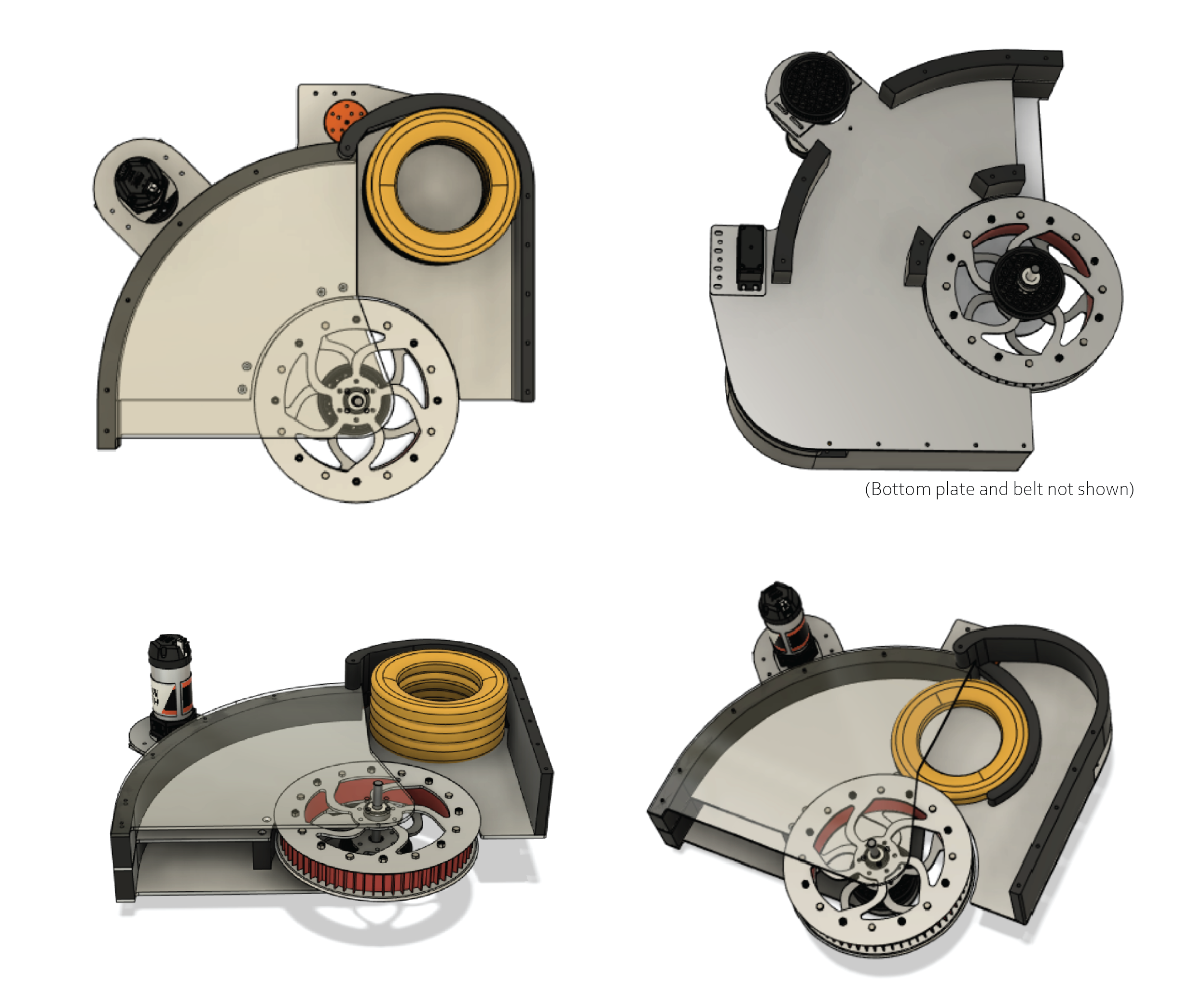
Next, we were able to discuss the ballistics calculations that this design inspired. In our previous two posts, we discussed the iteration of an equation we developed to model the inital velocity, muzzle velocity, RPM, and rotations/seconds of a ring launched from this flywheel, taking into account its circumference in order to determine the ideal angle of launch as well as how the PID values of the HD HEX motor on the flywheel needed to be tuned. Below is the slide from our presentation containing these values. Our ideal range for the horizontal distance of the robot is between 2-2.5m; this being said, we calculated all our values based on this range. Our equations were: Vertical: v0 = (0.47 - 0.5(-a)(t^2))/sinθ(t/2)) and Horizontal: v0 = (xF - 0.5(-a)(t^2))/cosθ (t/2)) While we couldn't perform a sanity check of these calculations at the time of their presentation, we found values from the average velocity of a frisbee to test the accuracy of our values.
Finally, as this was ongoing, Paul and Cooper were able to assemble and perform the first-ever launch of our flywheel launcher! Since this subsystem had already been pre-modelled with all the necessary plates pre-machined, they were able to complete its assembly and test within the 40 minutes of our presentation. While the actual video of the first launch can be found on DPRG's video of the presentation, a video of a launch recorded soon after our meeting can be found here:
At the end of this presentation, we were able to get tons of valuable feedback from DPRG - particularly about how to improve our testing process of the flywheel launcher. We anticipate that the equation we modelled earlier and those values are subject to change as our robot design becomes more sohpisticated and as we add more sources of error to the machine itself - in order to eliminate these confounding variables contributing to the launch and isolate the one that has the most effect (which we predict is the angle of launch itself), DPRG suggested that we use a Design of Experiments chart. A Design of Experiments chart is a system of organization that can be applied to virtually any machine to reflect the different variables that might affect its efficacy. More specifically, it identifies which variable had the greatest impact on a function and rank the variables in order of their influence. Applying a DOE to our flywheel launcher calculations would streamline our ability to identify which variable could have the greatest impact on our launch as we vary it by distance of launch, angle of launch, type of motor used, etc.
Next Steps
We are incredibly grateful to DPRG for giving us the opportunity to present our team and flywheel launcher to them for feedback. Our immediate next steps include continuing the testing of our flywheel launcher to see just how much we can improve driver control. Part of this includes fine-tuning our calculations and as we get deeper into the testing phase, we can check whether these equations work as well as they do in theory by using the DOE to identify any confounding variables. We plan on sending DPRG an updated version of our equation and calculations as we continue to periodically test and fine-tune our launcher.