A Deep Dive into the Shoulder and UnderArm
Tags: journal, think. innovate, and designPersonhours: 75
Describe our Implementation of the Shoulder and Turret Subsystems
With our primary game strategy for this season being to limit our movement around the playing field, the ability to quickly and easily rotate our intake and deposit systems is vital. Additionally, the ability to reach a variety of poles and scoring options is also crucial if we are to remain stationary. This is why we implemented a Turret and Shoulder on both versions of TauBot. This post will be a deep dive into the mechanics of both these subsystems on TauBot2.
First, let's talk about our Turret, which allows the Crane to move a full 360 degrees independently of the actual differential drivetrain. First off, we have the Slip Ring, a crucial part of the Turret since it allows the Turret to rotate continuously without interfering with the wire runs. Below is a simple breakdown of the new Turret assembly, which consists of turning curricular rings with ball bearings. Inside is a custom Nylon 3D-printed planetary ring used to drive the entire Turret and motorize it.
Finally, on top is a carbon fiber base plate upon which the entire Shoulder assembly rests. The Turret uses two main motors that synchronously drive its turning motion. The addition of another driving motor is what separates TauBot2 from the one lonely motor driving the TauBot Turret.
As seen in the image above, near the front, the two TauBot2 turret motors lay horizontally on the carbon fiber cover under the REV channels. These motors use bevel gears to direct power downward towards the turntable and the planetary gear, allowing it to turn twice as fast as its previous iteration.
On top of the REV channels, we have the entire Shoulder assembly, which is the basis for the Crane and allows our robot to score on various poles of all sizes from one stationary spot on the field. The two main functions of the Shoulder are to rotate the entire Crane up and down, and to power the extension of the linear slide.
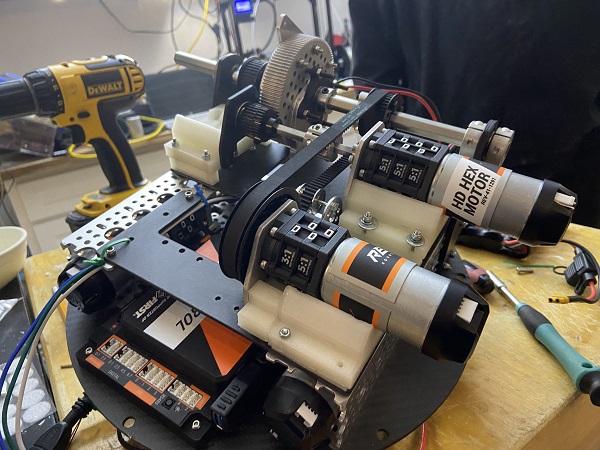
As you can see, the slide extension is controlled by the front motor and a belt drive. A gear ratio and second motor control the rotation. The gear ratio allows one motor to drive the entire elevation process and ensures easier positioning.
The axle housing the largest gear is also a co-axial joint, allowing it to drive the extension and rotation through two separate systems. The Shoulder uses the shaft as an axle, but the main arm rotation gear pivots freely due to two attached ball bearings. Overall, this allows us to combine multiple responsibilities into one design and save space.
The motor used for rotation and elevation is assisted by two springs and a custom-designed logarithmic spiral to provide a consistent upward force to counter the force of gravity on the extended Crane, helping to reduce torque.
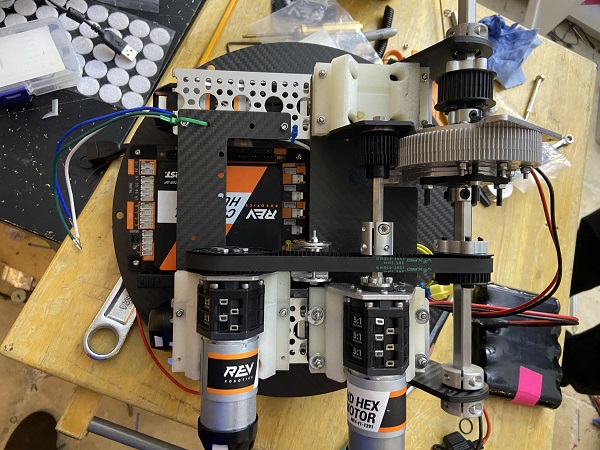
And that's a brief overview of the entire Shoulder and Turret system. This is also where our main Control Hub and our webcam are housed on the original version of TauBot. All in all, these two subsystems are crucial to the functionality of our robot and are the results of loads of careful and meticulous design by our team.