Errors Without Trials: Not Enough Testing With Our Sampler
Tags: control, innovate, mechanical, and softwarePersonhours: 9
We are on V4 of our Sampler, our intake designed for samples, but a lot of unforeseen issues have arisen due to a lack of effective testing after prototyping. V3 of our Sampler is falling apart because of shoddy assembly and a lot of tape as a last-ditch effort to hold it together, so we started rushing to get V4 of our Sampler completed and an effective servo on it without thinking about testing it off-robot. While the physical assembly of the new Sampler looked much cleaner than the last iteration, giving us hope for its functionality and ability to intake samples at a faster speed, getting it onto the robot and finally doing some testing crashed our hopes.
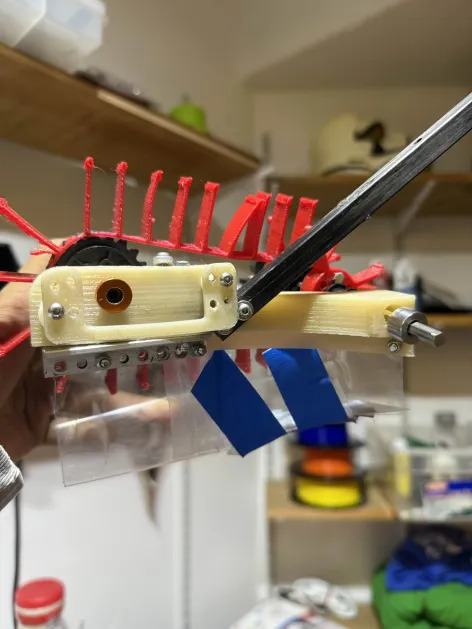
Main Problems:
- Beater bar tines are too stiff
- Angle is too steep and doesn't intake samples properly
- Color sensor mounted too far from Sampler walls and on wrong side of intake
- Beater belt sprockets not aligned properly, belt keeps slipping off
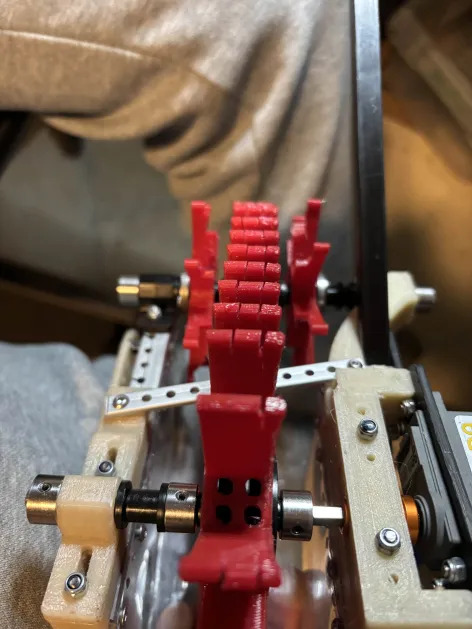
We've been having issues with our printers internal temperature sensor, which has caused our prints to come out differently. An issue we're having with V4 that we weren't having with V3 is the beater bar tines are too stiff. Because the beater bar tines are too stiff, instead of being flexible enough to bend backwards when the samples are coming through the intake channel, they're pushing the samples into the mats and are making it even more difficult to intake samples. As a short-term solution, we cut notches into each of the tines to make them more flexible.
The angle at which our CF tube is mounted to the Sampler is incorrect, meaning it was measured wrong from V3 of the intake. As this angle isn't working, we designed a 3D printed part which allows us to try out new angles, but have been having issues fitting into sizing with this new part. We are considering switching back to a pliable joint, using a hinge which can freely rotate as opposed to a completely rigid connection.
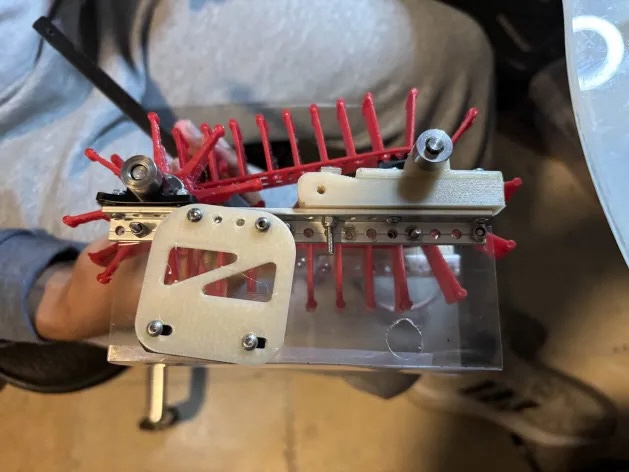
The color sensor is mounted too far from Sampler walls and is on the wrong side of the intake, but thankfully this is a quick fix. We sanded down the standoffs which are offsetting the color sensor so they align better with the walls and cut a new window for the color sensor on the appropriate side of the intake, using a thin layer of low-friction tape alongside the bottom of the hole so it doesn't hinder a sample's ability to travel through the intake channel.
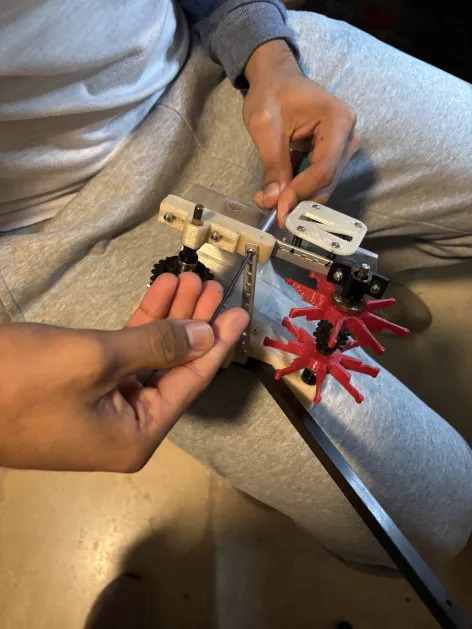
To fix the problem of the beater belt sprockets best, we decided to micro adjust the location of the sprockets but also discovered that the belt is too loose to self-correct. We removed a segment of the belt and re-welded it together to increase the tension so it stays on the sprockets better, and may also choose to add parts alongside the sprockets which help hold the belt in place. We also used a flat beam to keep the two sides of the intake channel in a fixed, tight position so the belt has less opportunity to slip.
Lessons Learned:
From now onwards, we won't shortcut our testing process as we prototype so we don't waste more time when we're supposed to be getting the subsystem onto the robot. We'll prioritize testing subsystems off-robot so coders can also have time to try getting subsystems coded separately before integrating them with the chassis and other subsystems and so we don't have to bootleg fixes when we're rushing to get progress made.